According to statistics, the annual consumption of raw materials used to produce ferrosilicon is around 2 million tons, but only 1.8 million tons of ferrosilicon can be produced, which means that this will be 200,000 tons of raw material losses. The raw materials for ferrosilicon are mainly quartz stone and steel scrap, of which the loss of steel scrap accounts for 80% of the total loss, which means that finding raw materials to replace steel scrap is the key to improving ferrosilicon production.
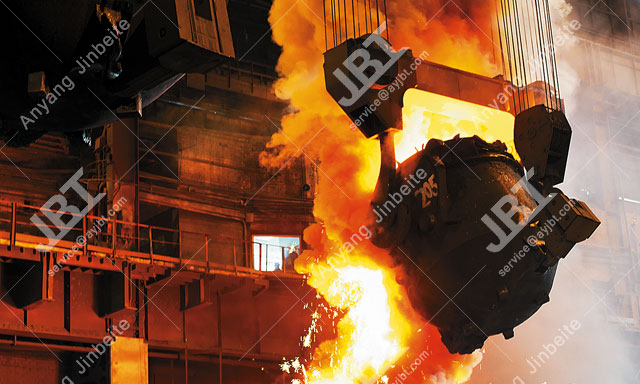
1. Ferrosilite
The use of ferrosilite as a raw material for replacing steel scrap can effectively produce a chemical reaction with SiC in the furnace, thus producing a much higher amount of iron than steel scrap. It can effectively stabilize the furnace condition and can significantly reduce the content of harmful elements such as aluminum and calcium in the steel melt to improve efficiency. Ferrosilite is the best raw material for ferrosilicon when the price increases due to the scarcity of steel chips.
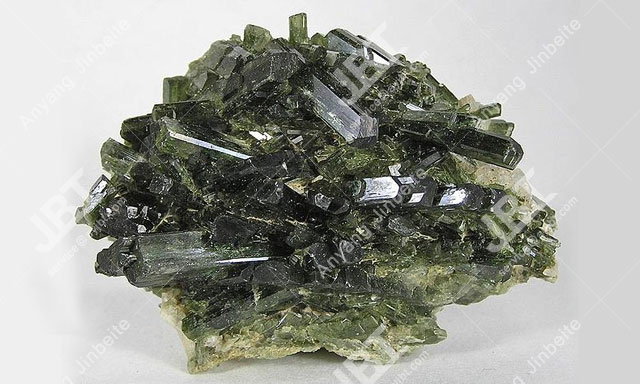
2. Mill Scale
The use of the Mill Scale will improve the condition of the raw material. It will improve the melting efficiency of raw materials, increase the speed of production and save electricity costs in the process of producing ferrosilicon. Mill Scale is the best raw material for our production of ferrosilicon, which can greatly reduce the production cost. The cost per ton of Mill Scale is only RMB 1,000, and compared with steel scraps, the use of Mill Scale eliminates the need for crushing and other processes. After calculation, every ton of ferrosilicon produced will reduce the cost by RMB 55.
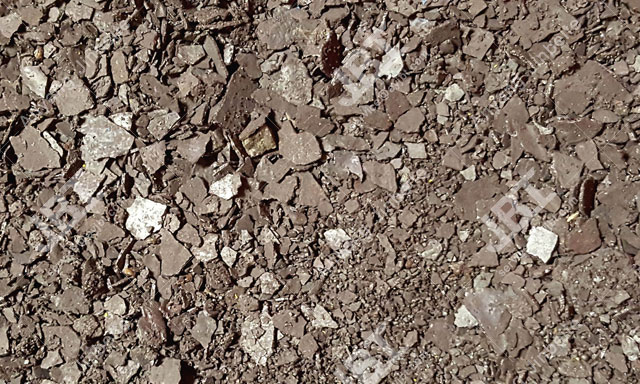
3. Pellet
Pellet, can be used as a raw material for the production of ferrosilicon. It will cause high electricity consumption, but the price of pellet is lower compared to steel scrap. Therefore, the pellet is still the best raw material to reduce the cost of ferrosilicon production in areas where the price of steel scrap is high.
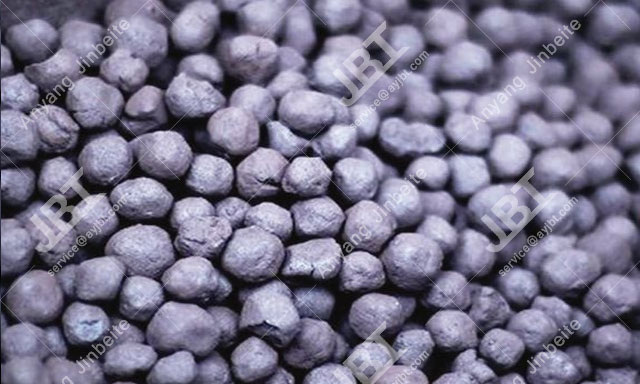
4. Scrap iron slag
Using scrap iron slag as a raw material for ferrosilicon production has several advantages. First, the pollution to the environment can be greatly reduced. Secondly, the cost can be effectively controlled, and the purchase price is relatively low, which is very suitable for manufacturers of large-scale production of ferrosilicon.