During the production of ferrosilicon or silicon metal, it is very easy to produce a large amount of dust that contains small amounts of silicon. Using professional equipment and technical means, this dust is processed to make microsilica.
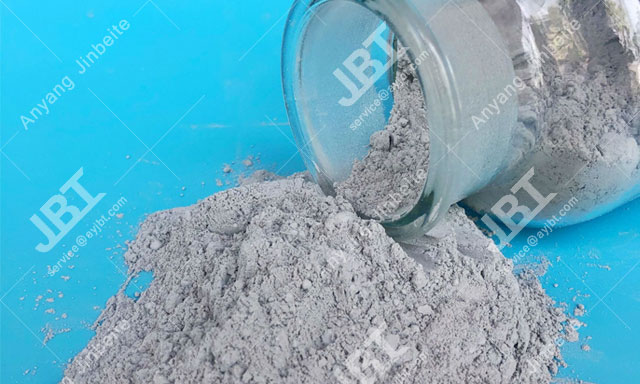
What is microsilica?
Strictly speaking, microsilica is a by-product of the production of ferrosilicon or silicon metal, rich in SiO2, with an average diameter of 0.1`0.3um, white, off-white, and gray in color. At present, the common microsilica is mainly produced by the production of silicon metal is more common, the color is mainly dark gray.
Classification
Classification by SiO2 content:
- SiO2≥85%
- SiO2≥90%
- SiO2≥92%
- SiO2≥97%
Classified by particle size or specific surface area:
- The median diameter is around 0.3um, the specific surface area value is 15-25m2/g, and almost all of the particles are ≤1um, and most of the microsilica in the world belong to this category.
- The median diameter of microsilica is around 0.1um or below, and the specific surface area value is ≥30m2/g, which is generally found in high purity microsilica , and is relatively rare.
- The median diameter is 0.5-2.0um, and the specific surface area value is 5-15m2/g, which is rare.
- The median diameter ≥2.0um is extremely rare, and the performance is poor.
Classification by density:
- 100-170kg/m3, easy to bond, poor conveying.
- 250-400kg/m3, basically no particles, the transportability is obviously improved, but unstable by the influence of temperature.
- 400-500kg/m3, microsilica begins to appear a large number of loose particles, not easy to bond, the transportability is better.
- 500-700kg/m3, the basic concrete microsilica is mainly hard particles (different products have different particle size and tightness), and the transportability is good.
Production Process
Using environmental protection equipment to treat the generated soot, without affecting the effect of environmental protection dust collection equipment, the main fan control parameters are adjusted to change the wind speed at all levels for different furnace conditions, change the pressure difference between the inside and outside of the filter bag, and control the filtration effect to achieve the purpose of adjusting the content of microsilica and other parameters. In addition, the dust collection equipment can also be upgraded by adding temperature-regulated air catcher sets, expanding the filtering area of the bag filter, etc., to change the SiO2 condensation time and molding properties of the entire dust collection system, and finally adjust the parameters of the microsilica.
Before the microsilica is sealed, it is necessary to ensure that the packaged microsilica is uniform in color and the product is free of lumps, and a numbered quality card is sewn onto the bag. This makes each bag of microsilica traceable, strengthen the accountability of operators, and facilitates identification in all aspects of production and storage, greatly enhancing product quality assurance.
When storing microsilica , different types of microsilica shall be stacked separately, and the same type of microsilica shall be stacked separately as a batch of products produced within a week. The storekeeper shall make records of the origin and stacking location of different batches of products. The laboratory personnel shall take a whole truck (25-30 tons) as a batch and then conduct a sampling inspection, the number of samples shall not be less than twenty bags, the weight of each bag shall not be less than 100g, and the samples shall be mixed evenly and sent for inspection. Each inspection is required to record the test time, index data, and other relevant information.
Applications
- In the field of concrete and refractory materials added to special refractory materials, the formation of the multi-layer protective layer in the oxidation, with good mechanical properties and resistance to high-temperature oxidation properties, special refractory materials added to ultra-fine microsilica, its fluidity, sintering, bonding, filling the pore properties have been improved to varying degrees. The structural density and strength are improved, the wear rate of the material is reduced, and the erosion resistance is enhanced.
- Application in binders and sealants, microsilica used in new binders and sealants can quickly form a network-like silica structure, inhibit the flow of colloid, curing speed is accelerated, can significantly improve the bonding and sealing effect.
- Applications in the electronics industry for electronic assembly materials, the main role is to waterproof, anti-dust, anti-harmful gas, slow down the vibration, prevent external damage, and stabilize the circuit. The amount of high purity ultra-fine and nano-silica filled in epoxy plastic sealing electronic materials reaches 70-90% or more, which can make it have excellent processability, small shrinkage, small coefficient of thermal expansion, good acid, and alkali resistance and solvent insulation, etc.
- Used in plastics and modified resins, microsilica is applied to plastics, especially in translucent plastic film, after adding ultra-fine silica, it greatly improves its strength, enhances toughness, improves waterproof performance, energy storage, heat preservation performance, etc. In plastic structural materials, after adding, its mechanical properties can be improved by 1 to 3 times. For modified resin-based composites, it can improve the strength, toughness, elongation, wear resistance, finish, aging resistance, and other properties of the composites.
- It is used in rubber materials for new rubber materials, which can make it excellent in dispersion and leveling, tear resistance, tensile resistance, aging resistance, and reinforcement. Compared with the middle and low end precipitated silica in the market, quartz powder is better than precipitated silica in SiO2 content (more than 99.6%), water content (less than 0.1%), product particle size, oil absorption and other main technical indicators.
How to use it?
When applied in cement paste and concrete, a good range of water-cement ratio will exist for microsilica , and generally, beyond this range, the improvement effect on hardened cement paste and concrete microstructure will be reduced. At the age of 3 d or 7 d of cement mortar, the strength of mortar specimens containing microsilica with a water-cement ratio less than 0.45 (water-cement ratio of 0.35, 0.40) decreases, while the strength of mortar specimens containing microsilica with a water-cement ratio equal to 0.45 or 0.50 increases; however, at the age of 28 d or 90 d of cement mortar, mortar specimens containing microsilica with a water-cement ratio less than 0.35, 0.40, 0.50 The strength is about the same; while the strength of mortar specimens containing microsilica (regardless of the content) with water-cement ratio equal to 0.45 is lower; when the water-cement ratio is equal to 0.50 and the amount of microsilica dosing is more than 27.5%, it has a significant effect on the later strength development of mortar.
Although, microsilica can effectively improve the microstructure of hardened cement paste and concrete, due to its small particle size and large specific surface area, the cement paste and concrete mixed with microsilica, with the increase of the admixture amount, the water demand increases and the self-shrinkage also increases. Since the concrete with microsilica may lead to self-shrinkage of concrete, and the concrete with microsilica is generally concrete with special requirements, therefore, the use of microsilica in concrete to harden the cement paste and concrete performance of the beneficial effects of the same time, must minimize the adverse effects brought about by microsilica, an effective way to solve this problem is to mix microsilica at the same time mixed with other volcanic ash Materials or other substances, so that they complement each other’s strengths and weaknesses to achieve better technical and economic results.
At present, more research is on the use of ultrafine slag and concrete microsilica blending or the use of fly ash and microsilica blending. Another field of application of microsilica more research is the use of silane on the surface of the microsilica pretreatment after blending into the cement paste or concrete or direct silane and microsilica at the same time blended into the cement paste or concrete, they can improve the workability of fresh cement paste and concrete, thereby improving the microstructure of hardened cement paste and concrete.
Specification
Model | SiO2 | Al2O3 | CaO+MgO | Na2O | Cl | NaOH | PH | LOI |
---|---|---|---|---|---|---|---|---|
SF-95 | 95% | 1.0 | 1.0 | 1.0 | 0.0055 | 1.0 | 5-7 | 6%max |
SF-92 | 92% | 1.0 | 1.0 | 1.0 | 0.0055 | 1.0 | 5-7 | 6%max |
SF-90 | 90% | 1.0 | 1.0 | 1.0 | 0.0055 | 1.0 | 5-7 | 6%max |
SF-85 | 85% | 1.0 | 1.0 | 1.0 | 0.0055 | 1.0 | 5-7 | 6%max |
Packaging & Storage
- Package in laminated plastic woven bags with the following specifications: 30kg/bag, 25kg/bag, 20kg/bag, or ton bag.
- Microsilica should be stored in a dry, rain-proof, and sun-proof environment, forbidden to be exposed to the sun for a long time, so as not to break the bag.
- Microsilica is not a dangerous good, transportation can be handled according to “Non-dangerous Goods Rules”.